These are types of products where each
individual item/unit has one (or many) unique properties. This could include a
serial number, the item’s weight, it’s condition etc. This is helpful when your
product may have different values depending on packaging, condition, physical
size/dimension, etc.
Currently Supported Properties
- Serial Number
- Weight
General UI
A handful of new buttons and interactions can be found
throughout the interface with the introduction of this new feature.
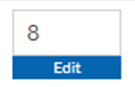

Generally isolated to quantity input boxes,
when a line item includes a serialized product, a new button will appear. When
clicked, it will open the editing window or selector window [both detailed
below] depending on the active workflow. Another of the new buttons is a blue
button with a barcode. This functions in exactly the same way, just used in
locations where the previous implementation was not suitable.
These buttons will appear when additional
information is required to handle the serialized products.
Editing Window
This window is used to
enter/edit the unique properties of a product. This window is used in all
inventory-in events which feature a serialized product.
There is a quantity indicator, generally this amount cannot be modified,
and it is set during a previous step of the workflow. However occasionally when
the workflow permits it, the quantity can be modified up or down in this
window.
Below that features a table with a number of rows matching the
quantity above. Each row contains input boxes for each unique property for the
specified product. Each row has an ‘x’ button at the end which clears that row.
At the bottom there is the save button which confirms and verifies
all entries and updates the data from the source the popup was generated from.
Selector Window
This window is used to
select products for all inventory out events which feature a serialized
product.
There
is a quantity indicator which updates based on how many products are currently
selected. With an alternate version for situations which require a fixed
quantity.
There is a location/warehouse dropdown selector which allows you to
view/select products from any location which has the desired product on hand. Occasionally
the location selector will be locked when the location has been set as read-only
in a previous step of the workflow.

Note: any selected products are reset
when changing locations. This is the intended effect as it is not possible to
have items from different locations in the same line item.
Below are the selected and available product
tables. The window will display all products available at the current location
and each of their unique properties. Select a product by clicking on the
corresponding select button to the left of each entry. Once selected, a new
section will appear at the top of the table which groups the selected products
together. A selected product can be removed by clicking on the remove button to
the left of the entry.
Tutorial
- Create a serialized product.
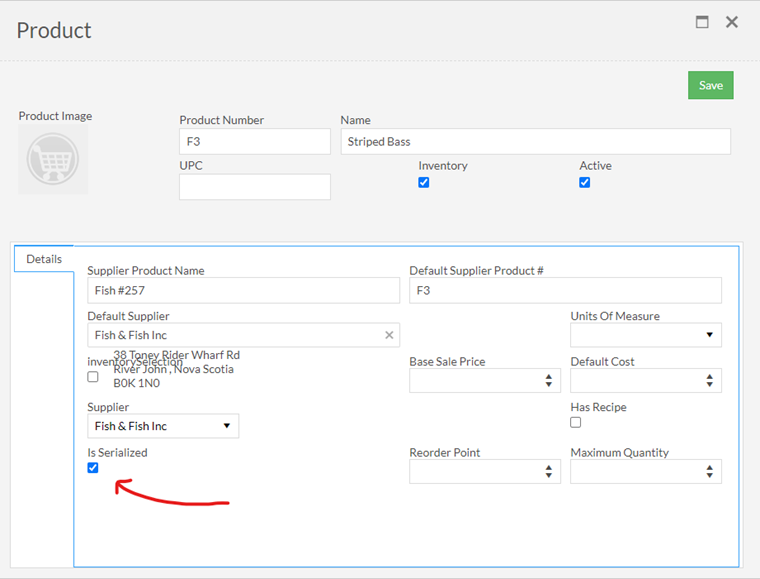
- Create a purchase order (identical
to any other product)
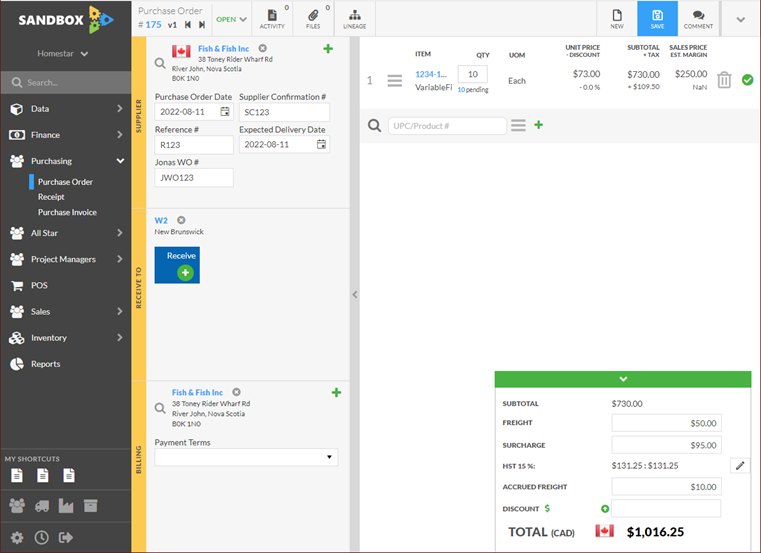
- Receive the purchase
order. Press the ‘edit’ button to open the input/editing window. A serial
number and weight are required for all products, you will not be able to
continue unless both are entered. The serial number and weight values can be
modified after the receipt has been created in case of any mistakes during the
input. It becomes locked and un-editable once the receipt has been marked as closed
or after a product from the lot has been sold/consumed.
The input/editing window can also be accessed from the regular receipt screen by clicking on the quantity box.
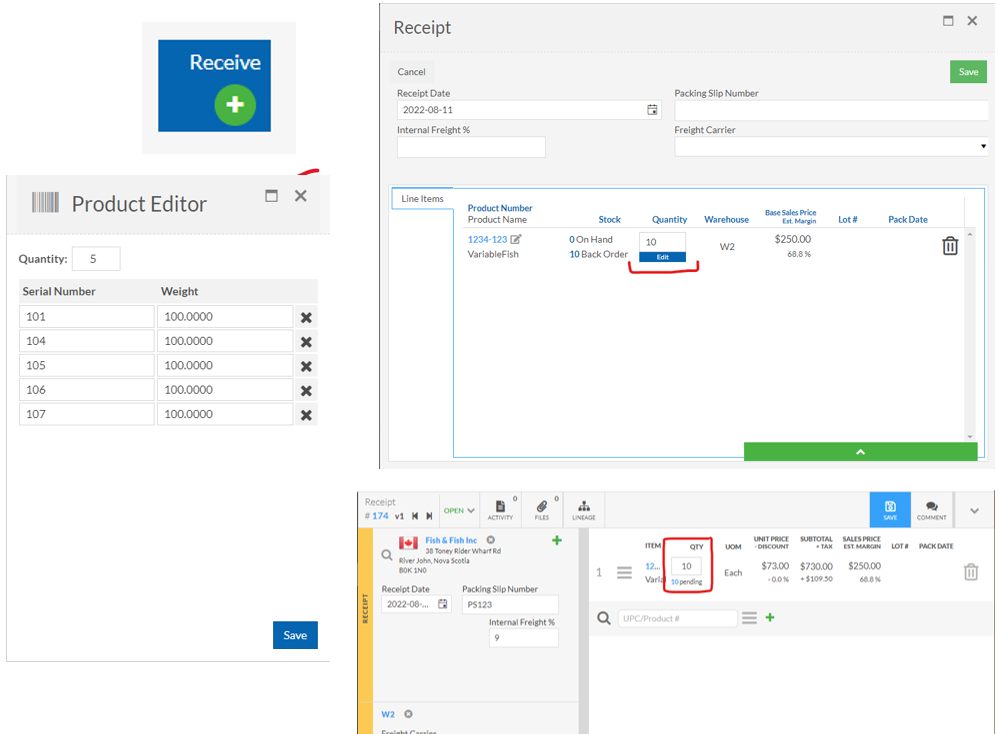
- Select a product for a POS sale, a Delivery, or any other
inventory out event. When selected, the product will move into a separate list
at the top to indicate which products are selected and which are still
available.
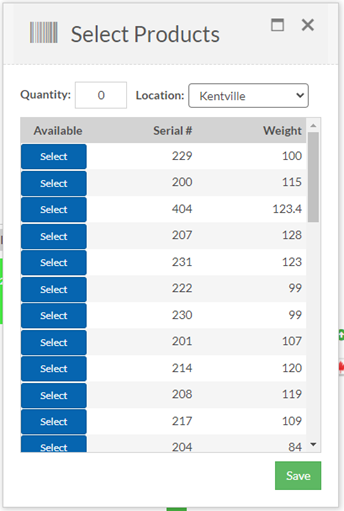

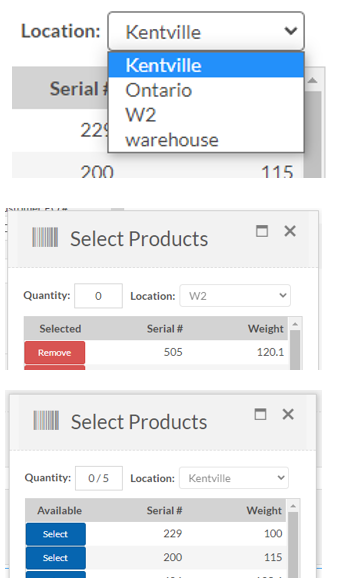